Capabilities
ENJOY SHORTER LEAD TIMES WITH A TOP TOOLING MANUFACTURER
As a leading tooling manufacturer with a history of high-volume tooling production, Pivot Precision has built up extensive internal production capabilities and capacity to deliver short lead times on complex, tight-tolerance, highly specified tooling down to 0.030-inch feature sizes with 0.0002-inch tolerances.
Our services include Swiss turning, CNC milling and lathing, vacuum and atmospheric heat treating, cryogenic hardening, annealing and surface finishing, assembly and testing, and customer inventory management, among others. Learn more about our capabilities below or contact our team for more information.
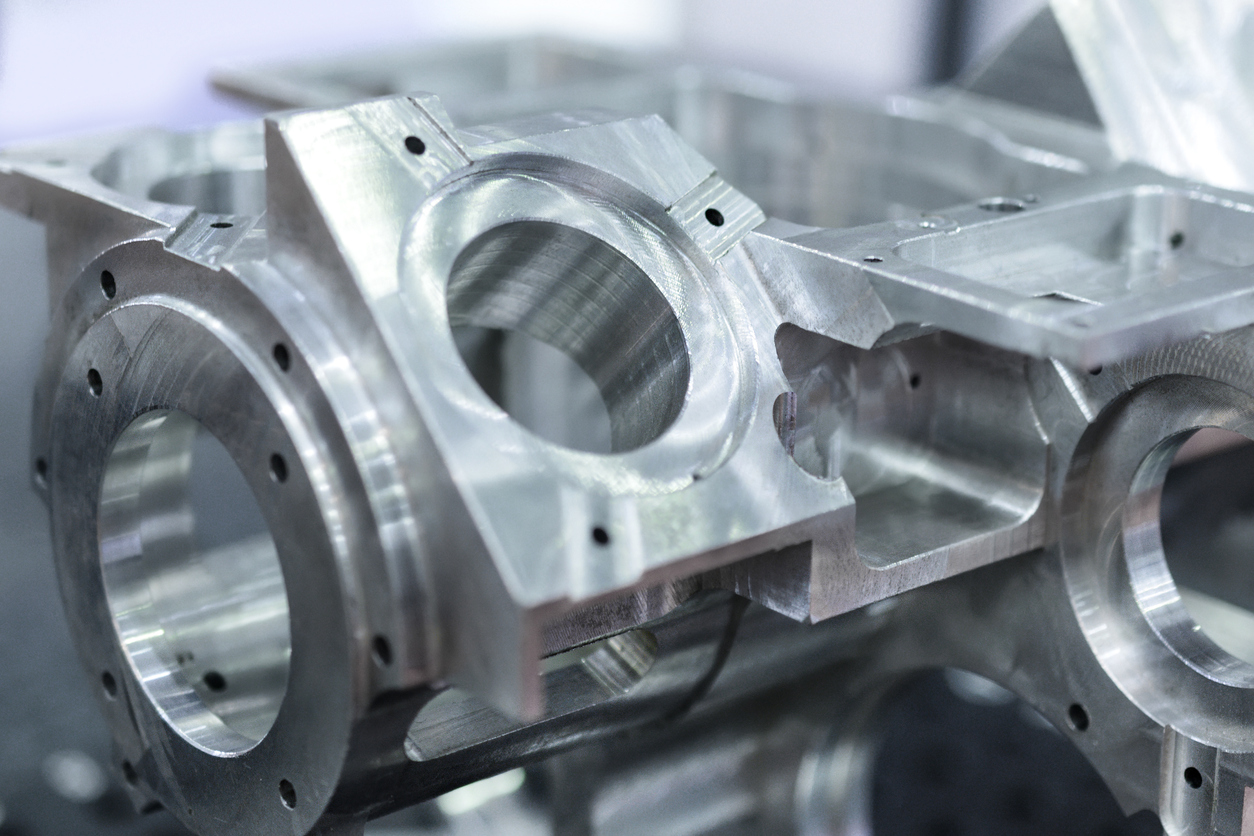
Our facility has state-of-the-art equipment that ensures your parts are manufactured quickly and built to tight tolerances. Learn more
Our various mills and lathes work around the clock to provide reliable, tight tolerance parts for your operation. Learn more
EDM machining is an ideal way to create small work pieces with complex shapes. Learn how we can support your needs here. Learn more
Grinding services are an ideal way to produce parts with tight tolerances. Learn how we can create your custom parts here. Learn more
Hard turning offers cost savings, faster turnaround times, and is more environmentally friendly than other machining methods. Learn more here. Learn more
When you need quality metal heat treating services, turn to Pivot Precision. Learn about our capabilities here. Learn more
When you want to give your tooling a professional look, turn to Pivot Precision for surface finishing services. Learn more